CIRCULAR CASE 3
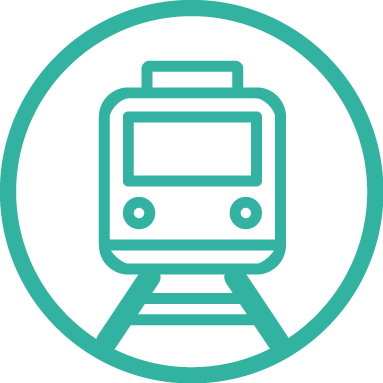
Transport infrastructure sector
Slovenia
From landfill to landslide stabilisation. Innovative composite of two recycling paper waste streams
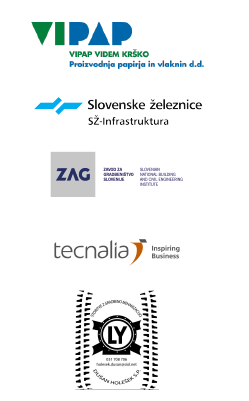
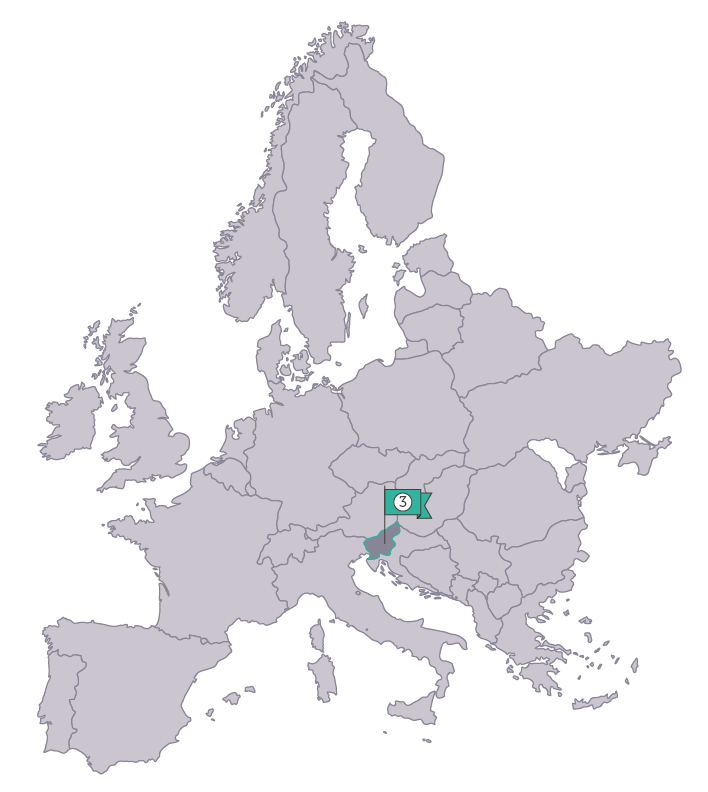
Current situation/ Problematic addressed
Pulp and Paper Industry VIPAP is a producer of newsprint and coated graphic papers. The main raw material used is recycled fibre obtained from recovered paper in the deinking process. As a consequence, three main waste streams are generated: Deinking Paper Sludge (DPS), Wastepaper Fly Ash (WPFA) and Wastepaper Bottom Ash (WPBA), producing annually, 25.000 tonnes of ash. Only a small percentage of this amount is used in civil engineering for low grade applications while most of them are still disposed to landfill, incurring in considerable costs.
Partners involved
VIPAP: Pulp and Paper industry generating the waste. It will improve the handling for both materials, optimizing the process to improve waste applicability.
ZAG: Research Institute in charge of the design of the innovative composite (WPA/DPS) in a defined ratio, characterization and testing at laboratory level for the demo case site. Technical support to get the required quality of the composite. Geo-mechanical characterization of the landslide.
SZ infrastructure (SZ): Railways infrastructure operator, End User
Dušan Holešek (DH): Construction SME in charge of the implementing the developed solution in the demonstration site.
TECNALIA: Environmental impact assessment and environmental monitoring support.
Alternative proposed:
A synergistic beneficial use of VIPAP’s waste materials can be proven in the field of renovation of the railway infrastructure. Along the last years, ZAG has been researching to find alternative cost-effective materials based on paper waste products. An innovative composite, with the market name MUDIPEL, made of DPA/DPS has been developed as a result. MUDIPEL is a composite material mixed from 70 % of deinking paper ash (DPFA with DPBA) and 30 % of deinking paper sludge (DPS). Material is compacted at optimal water content and maximum density. This material is light (< 1 t/m3), but could in time develop a considerable strength (>1 MPa at 28 curing days) and is easy to handle. It is a low permeability material. Wet paper sludge fibres allow the material to be transported over longer distances, which allows it to remain usable even far away from the paper mill. ZAG as a notifying body granted the Slovenian Technical Approval (STS) for using the Composite material MUDIPEL as a construction product.
DEMONSTRATION ACTIVITIES
Case Study 3 uses the ash coming from the energy recovery of paper waste combined with the sludge generated in the deinking process of the recycled fibres. The combination constitutes as a new backfill which replaces gravel material avoiding landfilling. The demonstration will take place in a section/area of 70m of length of the Slovenian railway. WPA/PSD composite will be filled in layers of about 15cm. These layers will be compacted separately and covered at the top with protective vegetation.
Demonstration
The gabion retaining walls will be filled will gravel material, as standard material for gabions. The WPA/DPS composite will be used as backfilling material between gabions and slope (unstable soil or rock). The composite will be mixed and installed properly, together with an adequate drainage system and the protective covering layer above the landslide. The slope stability will be calculated by numerical methods based on geotechnical properties determined in ZAG´s geo-mechanical laboratory and with onsite testing in the landslide area. The advantages of the innovative solution are:
Metres of length
cm Filled layers WPA/PSD
The advantages of the innovative solution are
Reduction of the wall section, using less gabions
Strengthening of the slope-gabions contact
Technical performance:
MUDIPEL is a composite material mixed from 70% of deinking paper ash (DPFA with DPBA) and 30% of deinking paper sludge (DPS). Material is compacted at optimal water content and maximum density. MUDIPEL is a light material (< 1 t/m3), with high shear properties (high friction of angle and cohesion), high uniaxial compression (>1 MPa at 28 curing days) and low coefficient of permeability (< 10-8 m/s). Under the load the material behaves elastically and allows smaller deformations.
Geomechanical characterization of the landslide will be determined with In situ tests (borehole drilling and borehole testing) and geomechanical laboratory tests to map and define the landslide behaviour. Quality control assurance programme consists of laboratory tests of the composite material (water content, density, dynamic modulus). Field tests will be done to check both the slope and the retaining wall stability (geometric and inclinometer measurements). Some KPIs will include: landslide movement (mm/day) and retention wall verticality. The workability of the new composite will be evaluated. It is expected to have enough workability time from the mixing at plant to its installation. KPIs will include workability period (in minutes), maximum bulk density (t/m3) and percentage of the maximum water content (%).
Environmental performance:
Leachability tests will be done before the implementation to assure that the composite complies with the Slovenian Environmental Regulation. After implementation, soil and water samples from the demo site will be periodically taken and compared with previous data.
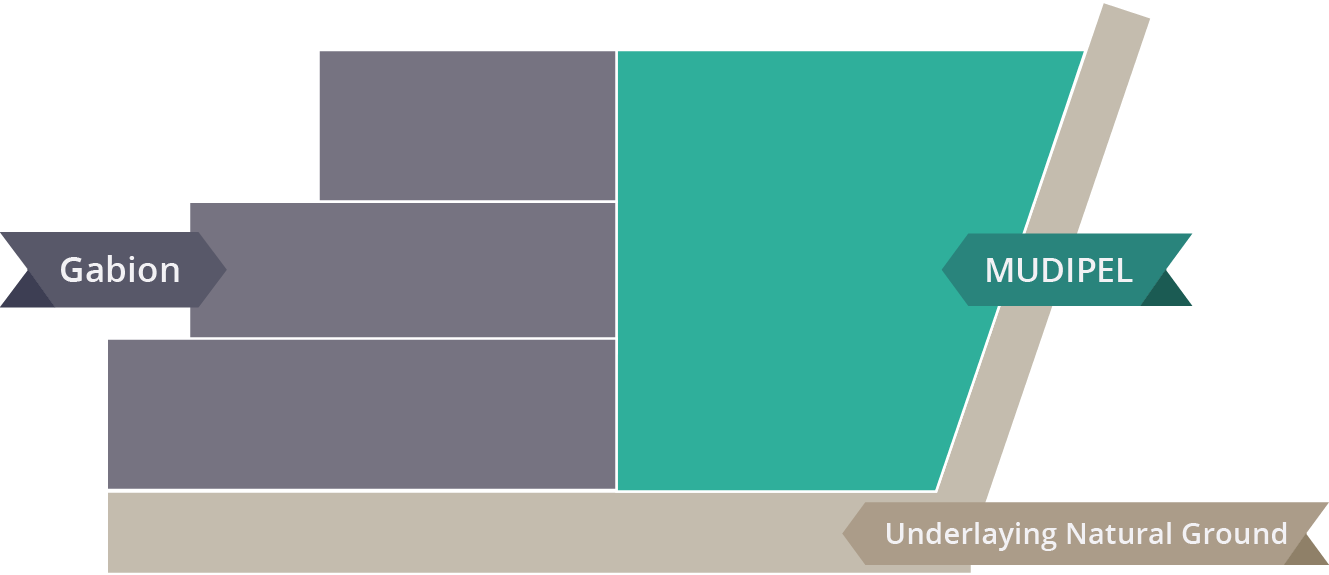
Quantification of the valorisation achieved during the project & Replication potential
%
of the gabions replaced
tonnes of the WPA/DPS used
During the project:
For the demo purposes, at least 50 tonnes of the WPA/DPS composite will be used as part of the retaining walls structural solutions, replacing up to 30 % of the gabions.
Replication:
The project can be easily replicated in the Slovenian railway network, as every year this kind of structures are constructed for slope stabilisation and the whole value chain is involved in the demonstration action.